Tool Post Grinders/How to choose |
|
Recommendations for the correct use of ADRI ToolPost Grinders |
|
A
- |
The ADRI Toolpost Grinders are supplied ready for
external grinding, with a plain wheel already mounted, balanced and dressed. The motor is normally
supplied for working in 220V - 60Hz mode (any other model will be shown on a card label attached to
the motor). |
B
- |
The choice of abrasive, grit size, grade structure and bond of the wheel, depending
on the material to be ground, should be made following the grinding wheel maker´s guide. The wheels
supplied with the ADRI Grinders have the following specifications:
ABRASIVE TYPE = WHITE ALUMINIUM OXIDE
GRIT SIZE = MEDIUM (60-46)
GRADE = MEDIUM -SOFT (K-J)
STRUCTURE = DENSE (6)
BOND = VITRIFIED
|
C
- |
To achieve maximum from a wheel, it´s speed is most
important, and for vitrified wheels the periphery speed should be between 25 and 35 m/sec. If not able to run
at these indicated speeds, for example when grinding small diameter bores, it is necessary to reduce wheel feed.
The spindle speed should be calculated in order to maintain the wheel´s periphery speed between 25-35 m/sec.,
which is achieved with different pulley combinations (See tables "Working Conditions for External and Internal
Grinding"). |
D
- |
LUBRIFICATION OF SPINDLES:
We use ISOFLEX LDS SPEZIAL A, from Kluber
Lubrication or similar.
Normally there is no need to lubricate
spindles because we use permanent grease.
If for any reason however, we recommend
utmost care when dismounting. All parts should be washed with white spirits and thoroughly dried before
lubrication and re-mounting.
All high speed spindles run hot but an
excess of grease will make them run very hot and may damage bearings. |
|
|
How to choose your ADRI Tool post Grinder |
|
Basically the choice is made taking into consideration the following points: |
1
- |
The type of job to be done. |
2
- |
The size of the lathe. |
|
1
-
Type of job to be done |
|
Toolshops - normally need a versatile grinder to carry
out all types of grinding, both
external and internal. A high degree of precision is normally required.
Indicated grinder : ADRI-RAE 0,75.
Mass production - needs a grinder with adequate power
to guarantee continuous work.
The ADRI RAS as large as can be fitted on the lathe is usually chosen.
External Grinding - choose the largest grinder that can
be fitted on to the lathe, which
means larger wheel and greater power, resulting in quicker and better finished jobs.
Internal Grinding - Usually the diameter of the internal
grinding wheel should be about
75% of the diameter of the hole to be ground. Use the larger ADRI-RAS grinder
compatible to the chosen grinding wheel taking into consideration the rotation of the
spindle.
|
|
2-
Size of the lathe |
|
Grinding is carried out with the spindle center, and
therefore the wheel center must
be perfectly lined up with the center of the piece to be ground.
The height "h" must be equal or larger than the distance
"F".
The practical chart will help you choose the appropriate
ADRI Toolpost Grinder.
"h" is the height considered from the center point to the
top surface of the compound
rest.
|
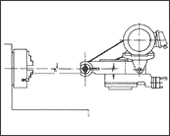 |
"h" |
F |
Model |
> 15
to 25
|
15 |
RAS 0,25 |
23 to
30
|
23
|
RAS 0,50
|
28 to
35
|
28,5
|
RAS 1,0
|
>35
|
35
|
RAS
1,5 and 2,0 |
|
|
The ADRI-RAE 0,75 Toolpost Grinder is appropriate for any type of lathe or job as it is manufactured with an adjustable
spindle holder. |
|
How to
achieve a good finish with the External Grinder |
|
1
- |
The Toolpost grinder must be securely fixed to the lathe, after
having assured that the wheel´s center height is the same as the piece to be ground. |
2
- |
The belt should be tensioned only enough to provide vibration free
drive. Over tight belts will induce extra strain on bearings. During storage slacken or remove belt. |
3
- |
Perfect parallelism must be kept between the spindle and the center
axis of the lathe. |
4
- |
Switch on the grinder, begin the grinding operation, dressing the
wheel when necessary. |
5
- |
When the plain wheel´s diameter is reduced to 3/4 of it´s original
size substitute the spindle´s pulley with a smaller one. |
6
- |
When the plaain wheel´s diameter reaches 1/2 it´s original size
substitute it for a wheel with the original diameter, also reverting to the original spindle pulley. |
7
- |
At this point and before returning to the grinding operation, it is necessary to balance the new plain
wheel, following these points:
A - Remove the Plain Wheel(PW) and Plain Wheel Flange (PWF) from the spindle.
B - Mount the ground tapered Balancing Arbor (BA) supplied with the grinder,in the flange PWF.
C - Place the unit on a Balancing Stand.
D - Move the counter weights(CW), in the tracks of the flange, until the grinding wheel rests in any position.
E - Mount the unit PW-PWF on the spindle.
F - Repeat steps A, B, C and D with the wheel already dressed.
G - Re-mount the unit PW-PWF and the wheelguard on the spindle and begin the grinding operation.
|
8
- |
For external work never change the motor pulley. |
9
- |
When fitting or removing pulleys and flange (PWF) onto/from the
spindle, use the 2 fixing screws, the extractor and hexagon keys provided. |
|