|
Cabeçotes/Multiplicadores de Velocidade |
Os Multiplicadores de
Velocidade ADRI-MAV são projetados principalmente para uso
em Centros de Usinagem Verticais, podendo também ser utilizados
Centros de Usinagens horizontal, Fresadoras CNC ou convencionais. São ideais para ferramentarias,
matrizes e moldes, retificação de furos de pequenos diâmetros
e trabalhos de acabamento. |
|
|
 |
5 modelos com cone ISO/BT-30, 40
ou 50 |
 |
O Cone é parte integral do cabeçote |
 |
Velocidades até 22.000 RPM |
 |
Engrenagens cônicas, temperadas e
retificadas |
 |
Ferramentas até 20mm de diâmetro |
 |
Componentes tratados e retificados |
 |
Relação de transmissão de até 1:6 |
 |
Fixação com pinças ER, ou outros
sob consulta |
|
|
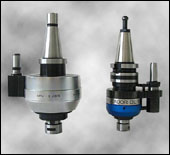
|
Bloco
Indexador
O funcionamento do cabeçote ADRI-MAV requer um Bloco Indexador que é montado na parte fixa do fuso da máquina. Este
Bloco Indexador é para posicionar o cabeçote sempre na mesma
posição e para desengatar o travamento.
Está disponível sob encomenda ou pode ser fabricado pelo
cliente de maneira que atenda as especificações da máquina.
|
|
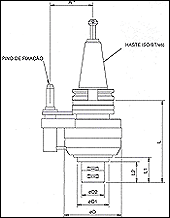
|
Código |
MAV-0 |
MAV-1 |
MAV-2 |
MAV-3 |
MAV-4 |
A* |
65 |
65 |
65 |
80 |
80 |
Cone |
30 |
40 |
40 |
50 |
50
|
ØD |
80 |
80 |
105 |
125 |
150 |
ØD1 |
44 |
44 |
55 |
62 |
100 |
ØD2 |
30 |
30 |
35 |
38 |
50 |
L |
125 |
125 |
135 |
145 |
150 |
L1 |
34 |
34 |
40 |
46 |
65 |
L2 |
25 |
25 |
30 |
31 |
36 |
Pinças |
ER-16 |
ER-16 |
ER-20 |
ER-25 |
ER-32 |
Diâm. máx.
ferramenta |
10 |
10 |
13 |
16 |
20 |
RPM máxima |
22000 |
22000 |
18000 |
15000 |
12000 |
RPM recomendado |
18000 |
18000 |
15000 |
12000 |
10000 |
Relação |
1 : 5 |
1 : 5 |
1
: 6 |
1
: 6 |
1
: 6 |
Peso incluindo
cone (Kg) |
3,3 |
3,7 |
5,8 |
8,0 |
8,0 |
|
HIGH SPEED CUTTING (HSC)
USINAGEM EM ALTAS VELOCIDADES |
A USINAGEM em ALTAS VELOCIDADES está cada dia mais difundida na indústria, sendo particularmente usada nos processos de Fresamento, Furação e Retificação. A sua aplicação é principalmente indicada para semi – acabamento e acabamento em materiais não – ferrosos. HSC, como é conhecida, substitui – se processos de poucos, lentos e pesados passes de usinagem para muitos, rápidos e leves passes. Algumas características que tornam o HSC mais vantajoso são enumeradas a seguir:
1 - Tempos de Usinagem muitas vezes menores, garantindo maior produtividade.
2 - Uma sensível melhoria obtida na qualidade superficial das peças.
3 - baixas forças de Corte resultando em menos força de usinagem, proporcionando ainda as seguintes vantagens :
• Sistema de fixção de peças não sofre grandes exigências de cargas, apresentando menos vibração durante o processo de usinagem.
• Quando empregadas elevadas relações “comprimento/diâmetro” da ferramenta, o desvio da haste da ferramenta é menor.
• Com o desvio da haste da ferramenta menor que o normal, o resultado é um menor erro de forma e um melhor acabamento superficial.
• As solicitações exercidas no fuso da Máquina – Ferramenta e outros componentes de máquina são menores, resultando em vida útil maior e menores custos de manutenção.
Alguns parâmetros e valores típicos de usinagem HSC são os seguintes:
4 - Profundidade de Corte entre 0,01 a 0,5mm
5 - Largura de Corte entre 0,05 e 4mm
6 - Avanço por Dente até 0,25mm
7 - Velocidade de Corte entre 280 e 465m/min para Alumínio e outros materiais não ferrosos equivalentes, tais como Latão, Bronze
8 - Velocidade de Corte entre 90 e 110m/min para aços e fundidos
Obviamente, um estudo pormenorizado de Processos de Usinagem deve ser realizado para levar a uma escolha ideal entre estes parâmetros.
Como já dissemos anteriormente, a Usinagem em Altas Velocidades é mais indicada para materiais não – ferrosos; a usinagem de materiais ferrosos, como os aços tratados ou não e o aço inox, por exemplo, apresenta outras características devido a alguns fatores considerados inconvenientes:
- A estrutura abrasiva de ferro cinzento ou nodular
- O aço inox pobre condutividade térmica
- As ligas de Níquel, Cromo e Titânio que tornam o aço mais duro
INFORMAÇÕES COMPLEMENTARES
A Usinagem em Altas Velocidades e o seu sucesso dependem basicamente de cinco componentes, interagindo entre si para garantir o resultado desejado. Esses cinco componentes são: o Fuso da Máquina – Ferramenta, o Cone de fixação, o Multiplicador Hi – Speed, a Fixação da Ferramenta de Corte e a Ferramenta de corte em si.
Uma confiável fixação entre o Fuso da máquina e o Cone é de suma importância, pois, a partir desta fixação em maior parte é garantida a estabilidade de usinagem. Os Cones mais utilizados são os manufaturados conforme as normas internacionais DIN, ISO e BT.
Estudos realizados têm demonstrado que a superfície de contato entre o Fuso e o Cone mantem – se a 100% (contato integral) até uma velocidade de aproximadamente 22000 rpm. Acima deste valor há uma perde de contato, chegando a somente 37% (contato parcial) para uma rotação de 25000 ou mais. O mesmo principio vale para o contato entre o eixo do Multiplicador e a Pinça de Fixação. Esta é uma das razões por qual o Cabeçote Multiplicador Hi – Speed Adri foi desenvolvido para atingir 22000rpm. É a sua segurança.
Por sua vez, a fixação de corte é de grande responsabilidade, pois a precisão de Multiplicador, estando dentro de uma concentricidade de 0,05mm, exige uma fixação de ferramenta também com precisão. Para esta finalidade a Pinça tipo ER é a mais utilizada. (Ver Pinças ER Din 6499 B). É a mais flexível das fixações de ferramentas, porém, alguns cuidados devem ser tomados com as Pinças tipo ER :
1 - A precisão de seu usinagem vai depender da Classe de Pinça ER que está utilizando. Analise bem qual é a classe mais adequada para seu serviço.
2 - O maior cuidado deve ser tomado na hora de trocar as Pinças conforme a necessidade de seu serviço, pois a troca e correta fixação depende da habilidade do operador. A precisão do seu serviço vai depender desta correta fixação.
3 - Certifique – se da procedência das Pinças ER. Compre somente Pinças fabricadas conforme a norma DIN 6499 B.
Outro fator que merece destaque é de que qualquer que seja a rotação, a mesma provoque a chamada “Força Centrifuga”. Esta força tende a jogar radialmente qualquer componente em rotação, incluindo a ferramenta de corte. Esta força aumenta geometricamente em função da rotação.Para tentar manter esta força dentro de parâmetros aceitáveis, o uso de ferramentas inteiriças é recomendado invés das ferramentas com insertos. Em usinagens a altas velocidades, por exemplo, uma ferramenta de corte de 12mm de diâmetro pode girar aproximadamente 15000 rpm, enquanto uma ferramenta de 16mm pode girar a 7500 rpm.
Em resumo, para garantir a boa qualidade dimensional e superficial de uma peça é necessário OTIMIZAR O SISTEMA DE FIXAÇÃO.
|
|
|